Table of Contents
Introduction
Innovations that improve productivity, quality, and sustainability are driving a technological renaissance in the steel industry. At the heart of this transformation is the adoption of digital twins.
Digital twins is a sophisticated, virtual modeling technology that enables steel manufacturers to simulate and optimize their operations with unprecedented accuracy. This steel fabrication approach is revolutionizing the steel rolling process and setting new standards for precision and efficiency in the industry.
By creating a digital replica of physical assets and processes, manufacturers can gain valuable insights, predict maintenance needs, and make data-driven decisions in real time.
How Digital Twins Reshape Steel Production?
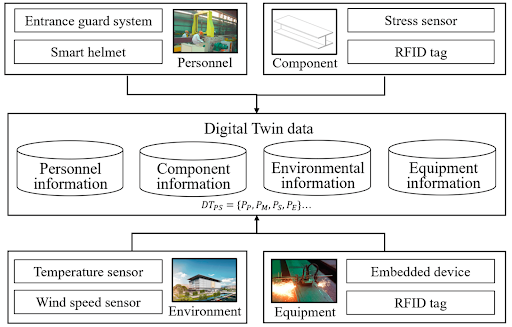
Digital twins introduce a revolutionary way to manage complex steel manufacturing processes by creating dynamic, virtual counterparts of physical assets. Unlike traditional static models, digital twins continuously capture data, allowing real-time monitoring, analysis, and simulation of steel manufacturing equipment, machinery, and production lines.
- These digital models facilitate an interactive link between the physical and digital realms, capturing every nuance of the manufacturing process, from machinery vibrations to environmental conditions.
- By harnessing the power of digital twins, steel manufacturers can optimize production efficiency, predict maintenance needs, and minimize downtime.
- This technology enables proactive decision-making and predictive maintenance strategies to enhance overall productivity and profitability in the steel industry.
- Digital twins provide operators and engineers with insights into equipment health, operational conditions, and system performance through continuous data streams from embedded sensors and connectivity.
In addition, this virtual counterpart enables scenario testing and process optimization, where manufacturers can adjust parameters like pressure, temperature, or material composition in the digital twin to find ideal production settings without ever affecting physical equipment.
The capacity to model “what-if” scenarios drives faster innovation cycles and allows for safer, data-backed decision-making.
Predictive Maintenance and Simulation

Digital twins are becoming essential tools in optimizing steel manufacturers processes, especially in predictive maintenance. By creating real-time virtual replicas of critical machinery, digital twins offer a detailed view of equipment health.
When integrated with predictive analytics, these digital twins can forecast potential failures, allowing for proactive maintenance before breakdowns occur.
This predictive approach has proven beneficial, as seen in steel plants that use digital twins for blast furnaces, allowing them to predict wear on essential components and plan repairs during scheduled downtimes.
- Overall, the use of digital twins in steel manufacturing has resulted in increased efficiency, reduced downtime, and cost savings.
- With the continuous advancements in technology, the potential applications of digital twins in predictive maintenance are vast and promising for the industry.
- The ability of digital twins to simulate process conditions also opens new avenues for production optimization.
- For example, steel mills use digital twins to experiment with rolling speeds and pressures, identifying conditions that reduce energy consumption while maintaining high-quality output.

Additionally, virtual replicas track resource usage across the production cycle, from raw materials to energy, helping manufacturers identify areas for improvement and implement changes to reduce costs and environmental impact.
In streamlining production workflows, digital twins play a crucial role. They enable manufacturers to follow materials and products through each stage, identifying bottlenecks and improving the flow of production.
For instance, a steel fabrication facility leveraged digital twins to monitor material movement, ultimately reducing lead times and increasing productivity by allowing agile decision-making in real time.
Strengthening Quality Control with Digital Twins in Product Monitoring
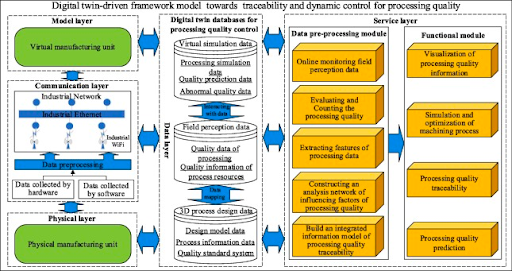
Digital twins have significantly elevated the standards for quality control in steel manufacturing. By allowing real-time monitoring and capturing critical data points, digital twins enable early detection of potential defects, deviations, and irregularities in the manufacturing process.
- Steel rolling process data-driven approach supports a proactive response to quality issues, reducing the likelihood of costly recalls or reworks.
- Leveraging digital twins in product monitoring also enhances predictive maintenance capabilities, ensuring optimal performance of equipment and minimizing downtime. This proactive approach ultimately leads to improved overall product quality and customer satisfaction.
- Digital twins provide a constant feedback loop that quality control teams can use to assess critical variables such as temperature, material composition, and pressure.
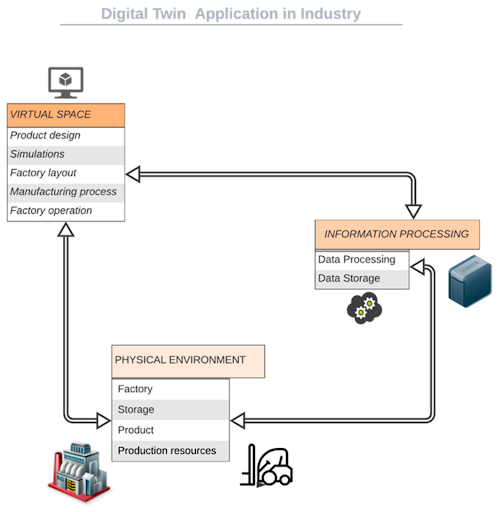
Real-world examples show how digital twins have enabled companies to quickly address deviations from quality standards, thereby enhancing product reliability and consistency.
This integration of virtual monitoring tools is reshaping quality control strategies, ensuring that steel manufacturers consistently meet stringent quality benchmarks.
Enhancing Operational Efficiency: Supply Chain, Inventory, and Workflow Management

Digital twins are streamlining the operational efficiency of manufacturing in steel mills beyond the production floor. They offer real-time transparency across the supply chain, tracking the movement of raw materials, work in progress, and finished products.
End-to-end visibility enables manufacturers to respond quickly to supply chain changes, optimize inventory levels, and reduce production delays.
- By utilizing digital twins, steel manufacturers can also improve workflow management by identifying bottlenecks and inefficiencies in the production process.
- The data-driven approach allows for proactive decision-making and continuous improvement in operational processes.
- Inventory management, for example, benefits from the insights digital twins provide on stock levels and demand fluctuations.
- Real-time data helps manufacturers prevent both stockouts and excess inventory, optimizing resource allocation and reducing waste.
Moreover, workflow coordination is enhanced by the synchronized monitoring of production lines, which reduces bottlenecks and facilitates the smooth flow of materials through each stage of the manufacturing process.
With this enhancement of agility and responsiveness, digital twins enable steel manufacturers to operate more efficiently and compete in a demanding market.
Addressing Challenges in Digital Twin Integration
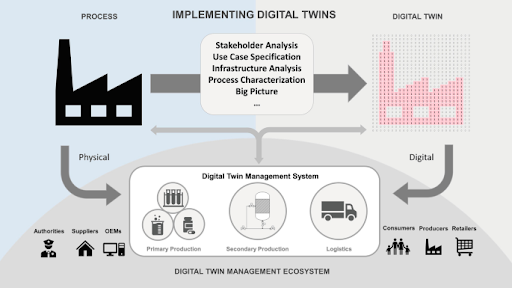
While digital twins offer remarkable benefits, several challenges must be overcome to maximize their potential in steel factories. One primary concern is data security, as real-time data flows often involve sensitive operational information.
- To mitigate this, manufacturers need robust cybersecurity measures, including encryption and access controls, to protect against cyber threats.
- Additionally, interoperability between different systems and platforms can pose a challenge when integrating digital twins into existing processes.
- Manufacturers must ensure that data can flow seamlessly between various software and hardware components to fully leverage the capabilities of digital twins.
- The integration of rolling mills and digital twins with existing systems is another challenge, as seamless connectivity between digital twins and legacy systems requires careful planning.
Open standards and middleware solutions can facilitate this integration. Workforce training is equally critical, as the technology requires personnel skilled in data analysis and digital systems.
Training initiatives and continuous education help bridge this skills gap, ensuring that employees can fully leverage digital twin capabilities.
Emerging Trends in Digital Twin Technology

Greater integration with technologies like artificial intelligence (AI), machine learning (ML), and advanced analytics will be great for digital twins future in the steel manufacturing industry.
This enhancement of algorithms improves the predictive and analytical capabilities of digital twins, allowing for even more accurate forecasting of equipment performance and production outcomes.
- The convergence of digital twin technology with AI and ML enables a proactive, intelligent approach to problem-solving, further driving efficiency and resilience in manufacturing.
- By harnessing the power of these technologies, steel manufacturers can optimize operations, reduce downtime, and ultimately increase profitability in steel manufacturing.
- The integration of AI and ML with digital twins also opens up possibilities for continuous improvement and innovation in the industry. Digital twins also support the steel industry’s sustainability goals.
The provision of a real-time view of energy consumption, emissions, and resource use empowers manufacturers to make data-driven decisions that reduce their environmental impact.
As the industry continues to evolve, digital twins will play a pivotal role in balancing operational excellence with environmental responsibility in steelworking.
Conclusion
Paving the way for a sustainable and technologically advanced steel industry, the integration of digital twins in steel manufacturing processes is proving to be a game-changer. The incorporation of digital twins into steel manufacturing is transforming the industry, enabling a future of increased precision, agility, and sustainability.
These virtual replicas not only optimize production processes and quality control but also streamline operations, making steel manufacturing more competitive. While facing challenges such as data security and integration complexity, the benefits of digital twins combined with advances in AI and machine learning position the industry for a promising future. Through the use of these tools, steel manufacturers are not just adapting to technological change; they are leading the charge toward a sustainable and technologically advanced future.
Deepak Wadhwani has over 20 years experience in software/wireless technologies. He has worked with Fortune 500 companies including Intuit, ESRI, Qualcomm, Sprint, Verizon, Vodafone, Nortel, Microsoft and Oracle in over 60 countries. Deepak has worked on Internet marketing projects in San Diego, Los Angeles, Orange Country, Denver, Nashville, Kansas City, New York, San Francisco and Huntsville. Deepak has been a founder of technology Startups for one of the first Cityguides, yellow pages online and web based enterprise solutions. He is an internet marketing and technology expert & co-founder for a San Diego Internet marketing company.